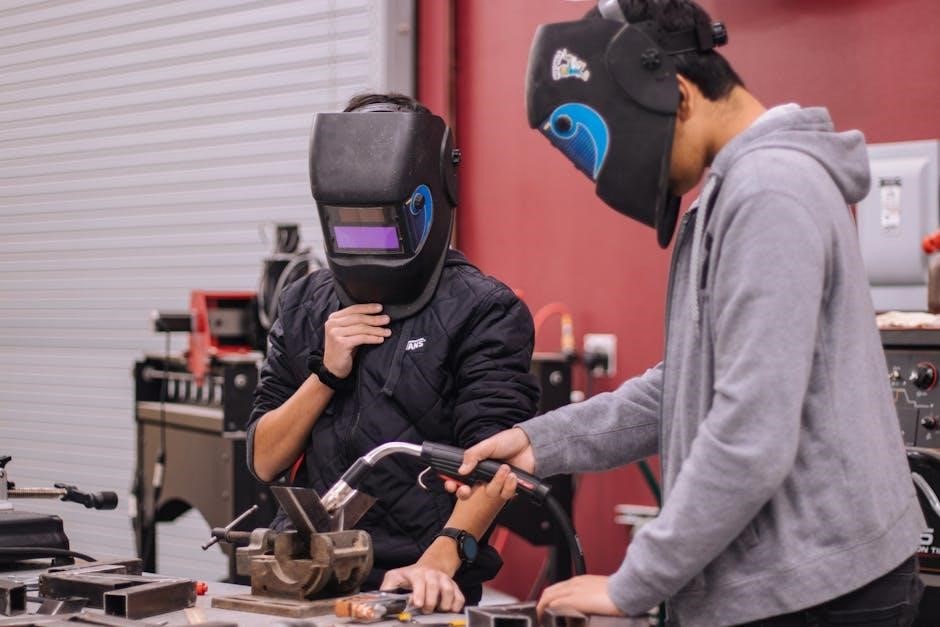
This section introduces essential welding tools and equipment, highlighting their roles in various welding processes. It emphasizes safety, efficiency, and the importance of proper equipment selection for optimal results.
1.1. Overview of Welding Processes
Welding processes vary widely, each requiring specific tools and equipment. Shielded Metal Arc Welding (SMAW) uses a consumable electrode covered in flux. Gas Metal Arc Welding (GMAW), or MIG welding, employs a continuous wire electrode. Gas Tungsten Arc Welding (GTAW), or TIG welding, utilizes a non-consumable tungsten electrode. Plasma welding and cutting use ionized gas for precise, high-temperature applications. Each process demands unique tools, such as electrodes, welding machines, and shielding gases. The choice of process depends on the materials being welded, desired strength, and the environment. Proper equipment selection ensures efficiency, safety, and quality. Understanding these processes is crucial for assembling the right tools and equipment, as detailed in the welding tools and equipment list PDF. This guide helps users identify the necessary tools for their specific welding tasks, ensuring optimal results across various applications.
1.2. Importance of Proper Tools and Equipment
Proper tools and equipment are essential for ensuring safety, efficiency, and high-quality results in welding. Using the right tools prevents accidents, enhances precision, and extends equipment lifespan. Safety gear like helmets, gloves, and goggles protects welders from hazards such as UV radiation and sparks. Correct machinery, such as MIG, TIG, or ARC welders, ensures compatibility with specific welding processes. Consumables like electrodes and shielding gases are critical for maintaining weld integrity. Without the appropriate tools, weld quality may suffer, leading to structural weaknesses or rework. A well-organized welding tools and equipment list, such as the one provided in the PDF, helps welders prepare adequately for projects, reducing downtime and improving productivity. Investing in quality tools is a necessity for both amateur and professional welders to achieve consistent, reliable outcomes.
1.3. Safety Considerations
Safety is paramount in welding, requiring meticulous attention to equipment and practices. Proper personal protective equipment (PPE) like helmets, gloves, and safety goggles shields welders from sparks, heat, and harmful radiation. Fire extinguishers and clean workspaces are crucial to prevent accidents. Fume extraction systems reduce inhalation risks, while first aid kits ensure quick response to injuries. Regular maintenance of tools and machinery is essential to avoid malfunctions. A welding tools and equipment list, as outlined in the PDF, helps ensure all safety gear is on hand. Adhering to safety protocols minimizes hazards, protects health, and maintains a productive environment. Prioritizing safety fosters a culture of responsibility, safeguarding both the welder and surrounding personnel.
1.4. Purpose of a Welding Tools and Equipment List
A welding tools and equipment list serves as a comprehensive guide, ensuring all necessary items are available for various welding processes. This list, often provided in PDF format, helps in organizing and maintaining tools, preventing shortages during projects. It includes PPE, hand tools, power machinery, and consumables, aiding in preparation and execution. The list assists in budgeting, inventory management, and compliance with safety standards. By having a clear inventory, welders can operate efficiently, reduce downtime, and maintain consistency in work quality. The PDF format makes it easily accessible and shareable, ensuring everyone involved is well-prepared. A well-structured list is indispensable for professionals and novices alike, fostering productivity and safety in welding environments.
Personal Protective Equipment (PPE)
Personal Protective Equipment is crucial for safeguarding welders from heat, sparks, and harmful fumes. Essential items include welding helmets, gloves, safety goggles, and respirators to ensure optimal protection during welding processes.
2.1. Welding Helmets and Lenses
A welding helmet is a vital piece of PPE that protects the welder’s face and eyes from intense UV/IR radiation, sparks, and molten metal. Modern helmets feature auto-darkening lenses, which adjust their shade based on the welding arc’s brightness, ensuring constant eye protection without the need to flip the lens manually. These lenses typically offer a range of shades, from light for visibility when not welding to dark for arc protection. Some helmets also come with additional features like adjustable sensitivity and delay controls, allowing customization for different welding environments. Fixed-shade lenses are another option, providing consistent protection but requiring the welder to lift the helmet when not actively welding. Regular maintenance of the lens, such as cleaning and replacing scratched or damaged lenses, is essential for maintaining visibility and protection. Helmets with a wide viewing area and lightweight design enhance comfort during long welding sessions. Properly fitted helmets ensure safety and prevent fatigue, making them indispensable in any welding setup.
2.2. Welding Gloves
Welding gloves are essential protective gear designed to safeguard a welder’s hands from extreme heat, sparks, and electrical shock. Typically made from durable materials like leather or heat-resistant synthetics, these gloves provide excellent insulation against high temperatures. They also offer protection from ultraviolet (UV) and infrared (IR) radiation emitted during welding processes. Welding gloves are designed to be thick yet flexible, allowing for dexterity and grip while handling welding tools or electrodes. Some gloves feature reinforced palms and cuffs for added protection against spatter and abrasions. They are a critical component of personal protective equipment (PPE) in welding, ensuring the welder’s hands remain safe and comfortable throughout the process. Properly fitted gloves also reduce the risk of accidents caused by slippery handles or inadequate grip. Regular inspection and maintenance of the gloves are recommended to ensure they remain effective and safe for use.
2.3. Leather Jackets and Sleeves
Leather jackets and sleeves are vital protective gear for welders, shielding the torso and arms from sparks, spatter, and heat. Made from heavy-duty leather, these garments offer excellent thermal resistance and durability. Jackets often feature high collars to protect the neck area, while sleeves extend coverage to the forearms. They are designed to withstand the harsh conditions of welding environments, preventing skin burns and clothing ignition. Some models include additional features like reinforced padding on high-risk areas or adjustable cuffs for a secure fit. Leather jackets and sleeves are recommended for both shielded metal arc welding (SMAW) and gas metal arc welding (GMAW) processes. They are a key component of a welder’s personal protective equipment (PPE), ensuring safety and comfort during prolonged welding sessions. Regular maintenance, such as conditioning the leather, is essential to prolong the lifespan of these protective garments and maintain their effectiveness.
2.4. Safety Goggles and Respirators
Safety goggles and respirators are indispensable components of a welder’s personal protective equipment, ensuring protection for the eyes and respiratory system. Safety goggles, often meeting ANSI Z87 standards, provide impact resistance and guard against sparks, spatter, and debris. They are designed to fit comfortably under welding helmets or as standalone protection. Respirators, available in half-face or full-face designs, filter airborne contaminants, including welding fumes and particles, to prevent inhalation of harmful substances. Many respirators feature replaceable filters, allowing customization based on specific welding environments. Both goggles and respirators are crucial for safeguarding health and preventing long-term occupational hazards. Proper selection and maintenance of these items are essential to ensure their effectiveness and longevity. Regular cleaning and replacement of filters or lenses are recommended to maintain optimal protection. Safety goggles and respirators are a necessity for any welding operation, enhancing both safety and workplace compliance. Their use is non-negotiable in professional and DIY welding settings. Always prioritize quality and fit when selecting these items.
Hand Tools for Welding
Essential hand tools include electrode holders, chipping hammers, and wire brushes. These tools facilitate electrode handling, slag removal, and surface cleaning, ensuring efficient and safe welding operations.
3.1. Electrode Holders
Electrode holders are crucial tools in welding, designed to securely hold and position welding electrodes. They ensure consistent electrical contact and prevent electrode slippage during the welding process. Available in various types, electrode holders are typically made of heat-resistant materials to withstand high temperatures. They are essential for both manual and automated welding setups, providing a safe and reliable way to manage electrodes. Proper use of electrode holders enhances welding quality and reduces the risk of accidents. Regular maintenance, such as cleaning and inspecting for wear, is important to ensure optimal performance. Electrode holders are a fundamental component in every welder’s toolkit, contributing to efficient and precise welding operations.
3.2. Chipping Hammers
Chipping hammers are essential tools in welding, used to remove slag and spatter from welds after the welding process. They typically consist of a forged steel head with a chisel or point on one end and a flat surface on the other. These tools are designed for durability and precision, allowing welders to clean and prepare the weld area effectively. Chipping hammers are available in various sizes and shapes to suit different welding applications. Regular maintenance, such as keeping the tool clean and storing it properly, ensures longevity. Safety precautions, like wearing safety goggles during use, are crucial to prevent injury from flying debris. Chipping hammers are indispensable for achieving smooth, professional-looking welds and are a must-have in every welder’s toolkit.
3.3. Wire Brushes
Wire brushes are versatile tools used in welding to clean and prepare surfaces before and after welding. They are designed to remove rust, dirt, slag, and spatter, ensuring a clean base metal for strong weld adhesion. Available in various sizes and types, wire brushes feature stiff or soft bristles made from materials like carbon steel or stainless steel. They are often used to clean welding electrodes and remove oxides from metal surfaces. Wire brushes are also used to finish welds by smoothing out rough edges or removing residual slag. Regular maintenance, such as cleaning the brush to prevent contamination, is essential for optimal performance. Wire brushes are a fundamental tool in both MIG and TIG welding processes, contributing to better weld quality and durability. Their portability and ease of use make them an indispensable asset in any welding setup.
3.4. Pliers and Vise Grips
Pliers and vise grips are essential hand tools in welding, used for gripping, bending, and holding objects securely. They are indispensable for tasks like tightening, loosening, and shaping metal components. Pliers come in various types, such as slip-joint, needle-nose, and locking pliers, each designed for specific applications. Vise grips, also known as locking pliers, provide a strong, adjustable hold, making them ideal for clamping materials during welding. These tools are crucial for maintaining control over small or irregularly shaped pieces, ensuring precise alignment and stability. They also help in handling hot or sharp edges, protecting the welder from potential injuries. Regular maintenance, such as cleaning and lubricating hinges, ensures optimal performance. Pliers and vise grips are fundamental to both MIG and TIG welding, enabling welders to manage materials effortlessly and achieve professional-grade results. Their versatility and durability make them a must-have in every welder’s toolkit.
Power Tools and Machinery
This section covers power tools and machinery essential for welding, including electric angle grinders, band saws, plasma cutters, and welding machines. These tools enhance precision, efficiency, and safety in various welding processes.
4.1. Electric Angle Grinders
Electric angle grinders are versatile power tools used for grinding, cutting, and polishing metal surfaces. They are essential for preparing weld joints and removing imperfections. Available in various sizes and power ratings, these grinders often come with interchangeable disks for different tasks. When selecting an angle grinder, consider factors like motor power, RPM, and disk size to ensure suitability for the job. Safety features such as anti-vibration handles and dust extraction systems are crucial for operator comfort and workplace safety. Regular maintenance, including replacing worn disks and ensuring proper tool balance, is necessary for optimal performance. Angle grinders are widely used in welding workshops and fabrication settings, making them a fundamental tool in the welding process. Their versatility and efficiency make them indispensable for both preparatory and finishing tasks in metalworking projects.
4.2. Band Saws and Cutting Tools
Band saws and cutting tools are essential for precise cutting of metal materials in welding applications. Band saws, with their continuous loop blades, offer clean and accurate cuts, minimizing waste and preparing materials for welding. They are commonly used for cutting pipes, tubes, and structural steel. Horizontal and vertical band saws are available, catering to different workshop needs. Additional cutting tools like hacksaws, bolt cutters, and reciprocating saws complement band saws, providing versatility for various cutting tasks. These tools ensure accurate material preparation, which is critical for strong and durable welds. Proper maintenance, such as blade replacement and alignment adjustments, is necessary to uphold cutting efficiency and safety. Band saws and cutting tools are indispensable in fabrication and welding workflows, enabling precise material preparation and enhancing overall productivity.
4.3. Plasma Cutters
Plasma cutters are advanced tools used for cutting metal by ionizing gas, creating a high-velocity arc that melts and vaporizes metal. They are highly precise, fast, and suitable for cutting various metal types, including steel, stainless steel, and aluminum. These cutters are ideal for intricate shapes and thin materials, making them popular in automotive repair, fabrication, and industrial settings. Modern plasma cutters often feature digital controls and portable designs, enhancing convenience and versatility. They are also used for cutting metal art and decorative pieces, offering clean, slag-free edges. Accessories like plasma nozzles and shielding gases are essential for optimal performance. Regular maintenance, such as cleaning the nozzle and ensuring proper gas flow, is crucial for extending the cutter’s lifespan and maintaining cutting quality. Plasma cutters are a valuable addition to any welding and fabrication workshop, providing precision and efficiency in metal cutting tasks.
4.4. Welding Machines (MIG, TIG, ARC)
Welding machines are the heart of any welding operation, providing the necessary energy for joining metals. MIG (Metal Inert Gas) welders are versatile and ideal for thin materials, offering high-speed, clean welds with minimal slag. TIG (Tungsten Inert Gas) welders are known for precision, used on intricate and high-quality welds, especially in aerospace and automotive industries. ARC welders, also known as Stick welders, are durable and suitable for outdoor conditions, capable of welding thick materials with a consumable electrode. These machines are available in various configurations, including multi-process models that support multiple welding types. Modern welding machines often feature advanced controls, such as digital displays and adjustable parameters, allowing for customized welding settings. Proper maintenance, including cleaning and regular servicing, is essential for optimal performance and longevity. Welding machines are a critical investment for any professional or hobbyist, ensuring consistent and reliable results across different projects.
Welding Safety Equipment
This section covers essential safety equipment for welding environments, including fire extinguishers, first aid kits, and fume extraction systems, ensuring a safe and hazard-free workspace.
5.1. Fire Extinguishers
Fire extinguishers are critical in welding environments to prevent and control fires caused by sparks, slag, or flammable materials. They must be easily accessible and suitable for the types of fires that may occur, such as Class A (combustible solids), Class B (flammable liquids), and Class C (electrical fires). Multi-purpose dry chemical extinguishers are commonly recommended for welding areas. Regular inspections and maintenance are essential to ensure functionality. Welders should be trained in their proper use and understand the PASS method: Pull the pin, Aim the nozzle, Squeeze the handle, and Sweep the area. Proper placement of extinguishers near workstations and exits is vital for quick response in emergencies. This equipment is a cornerstone of welding safety, protecting both personnel and property from potential fires.
5.2. First Aid Kits
A first aid kit is an essential component of welding safety equipment, designed to provide immediate care for injuries that may occur during welding operations. It should be easily accessible and stocked with basic medical supplies to address burns, cuts, and other minor injuries. Typical items include bandages, antiseptic wipes, gloves, eye wash solutions, and burn creams. The kit must be maintained regularly to ensure all supplies are up-to-date and not expired. In welding environments, where sparks and hot materials are common, having a first aid kit specifically equipped to handle burns is crucial. Employers and welders should familiarize themselves with the kit’s contents and know how to use the items properly. A well-stocked first aid kit not only promotes workplace safety but also ensures timely medical response, reducing the risk of minor injuries becoming more severe.
5.3. Fume Extraction Systems
Fume extraction systems are critical for maintaining a safe and healthy working environment in welding operations. These systems are designed to remove harmful fumes, particles, and gases emitted during welding processes, which can pose serious health risks to welders. Welding fumes often contain hazardous substances like metal particles, ozone, and nitrogen oxides, which can cause respiratory issues and other long-term health problems. Fume extraction systems typically consist of hoods, ducts, and filters that capture and neutralize airborne contaminants. They can be portable or installed as central systems, depending on the workshop size and specific needs. Regular maintenance of these systems is essential to ensure optimal performance and filter efficiency. By reducing airborne pollutants, fume extraction systems not only protect welders’ health but also contribute to compliance with occupational safety regulations. They are a vital component of any welding setup, ensuring a cleaner and safer workspace for everyone involved.
5.4. Work Area Lighting
Proper work area lighting is essential for ensuring visibility, safety, and precision during welding operations. Adequate lighting helps welders see the workpiece clearly, reducing eye strain and the risk of accidents. LED lights are commonly recommended due to their energy efficiency and minimal heat emission. Portable work lights are ideal for illuminating large workspaces or specific areas requiring focused attention. Additionally, magnifying lamps with built-in lighting can be useful for detailed work or inspecting welds. Many modern welding workshops also use motion-sensor lighting to enhance safety and convenience. Properly lit work areas not only improve productivity but also contribute to a safer environment by reducing tripping hazards and ensuring all tools and equipment are easily visible. Investing in high-quality lighting solutions is a critical aspect of setting up an efficient and safe welding workspace.
Consumables and Accessories
Consumables and accessories are vital for maintaining welding efficiency and quality. This includes welding electrodes, wires, fluxes, shielding gases, and tip cleaners, all essential for ensuring optimal weld performance and safety.
6.1. Welding Electrodes
Welding electrodes are essential consumables used in various welding processes, particularly in Shielded Metal Arc Welding (SMAW). They consist of a metal core coated with flux, which protects the molten weld area from atmospheric contamination. The electrodes are available in different types, such as E6010, E7018, and E308L, each designed for specific metals like steel, stainless steel, or aluminum. The selection of the correct electrode ensures proper weld penetration, strength, and resistance to corrosion. Electrodes must be stored in dry conditions to maintain their quality and performance. Improperly stored electrodes can become damp, leading to porosity in the weld. Regular inspection and replacement of electrodes are crucial for achieving consistent and high-quality welds; They are a fundamental component in the welding process, directly influencing the outcome and safety of the work.
6.2. Welding Wires and Fluxes
Welding wires and fluxes are critical consumables in welding processes such as MIG (GMAW), TIG (GTAW), and Flux-Cored Arc Welding (FCAW). Welding wires are continuous, bare or flux-coated electrodes fed through a welding gun or torch to create the weld. They are available in various materials, including steel, stainless steel, and aluminum, to match the base metal being welded. Fluxes, on the other hand, are used to shield the weld area from atmospheric contamination, reducing impurities and promoting a clean, strong weld. In processes like FCAW, flux is embedded within the wire, eliminating the need for external shielding gas. Proper selection of wires and fluxes ensures compatibility with the welding machine and base metal, achieving desired weld properties. Storage in dry conditions is essential to prevent moisture absorption, which can degrade weld quality. Regular inspection and replacement of these consumables are vital for maintaining consistency and performance in welding operations.
6.3. Shielding Gases
Shielding gases are essential in welding processes like MIG (GMAW), TIG (GTAW), and FCAW to protect the weld area from atmospheric contamination. Commonly used gases include argon, helium, and carbon dioxide (CO2), often in mixtures tailored for specific metals. Argon is ideal for TIG welding, providing a stable arc and clean welds. Helium enhances penetration depth and is often blended with argon for thicker materials. CO2 is cost-effective and commonly used in MIG welding for steel. Shielding gases prevent porosity and oxidation, ensuring high-quality welds. Proper gas flow rates and purity are crucial to avoid defects. Storage in high-pressure cylinders requires safety precautions, and regulators are used to control gas flow. Selecting the right shielding gas is vital for achieving desired weld properties and process efficiency. Regular monitoring of gas quality and consumption ensures consistent welding performance. This section highlights the importance of shielding gases in maintaining weld integrity and process reliability.
6.4. Tip Cleaners and Nozzles
Tip cleaners and nozzles are crucial for maintaining the performance and longevity of welding equipment, particularly in MIG and TIG processes. Tip cleaners remove spatter and debris from the welding tips, ensuring consistent arc stability and preventing porosity in the weld. Nozzles, or contact tips, are replaceable components that direct the welding wire and shield the arc. Proper maintenance involves regular cleaning and inspection to prevent wear and tear. Using the correct tip cleaner prevents contamination and extends the life of the contact tip. Nozzles vary in size and material to suit different welding applications, with copper or chrome-plated options being common. Regular replacement of worn nozzles avoids wire feeding issues and maintains weld quality. This section emphasizes the importance of tip cleaners and nozzles in optimizing welding efficiency and reducing equipment downtime. Proper care and selection are vital for achieving consistent, high-quality welds in various industrial settings.